At NPI Engineering, we distinguish ourselves by emphasizing a critical yet frequently underestimated facet of new product development.
Our expertise lies in bridging the gap between your design vision and the pragmatic realities of commercially available manufacturing, fabrication, and integration processes.
We specialize in guiding our clients through the entire New Product Introduction (NPI) process, meticulously tailoring component features to align seamlessly with commercially viable fabrication methods.
This strategic approach not only minimizes unnecessary costs but, more importantly, accelerates your time to market.
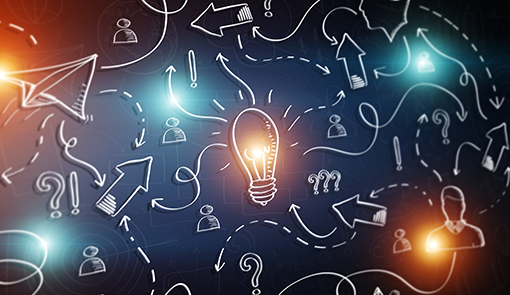
At NPI Solutions, we specialize in translating ideas into actionable plans. Our expertise lies in inputting functional specifications, establishing regulatory frameworks, strategizing sourcing directions, and forecasting useful product lifecycles.
- Input to Functional specification
- Setting regulatory framework
- Setting sourcing directions / strategy
- Estimating useful product lifecycle
- Estimating limits of future Production volumes
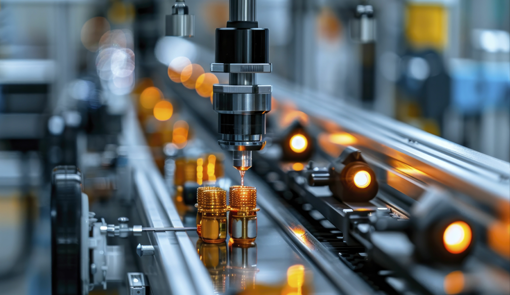
We specialize in facilitating product reliability analysis and reducing performance risks. Our team initiates safety risk mitigation processes in accordance with IAW 5.3 of SO-14971 guidelines. We meticulously select fabrication methods tailored to anticipated production volumes, ensuring efficiency and quality.
- Facilitate Product Reliability analysis and Performance risk reduction
- Initiate Safety Risk mitigation process (IAW 5.3 of ISO-14971)
- Selection of fabrication methods most suitable for anticipated volumes
- Manufacturability review on component level
- System level assembly Producibility review / mitigation (DFMA)
- Identify manufacturing / sourcing strategy
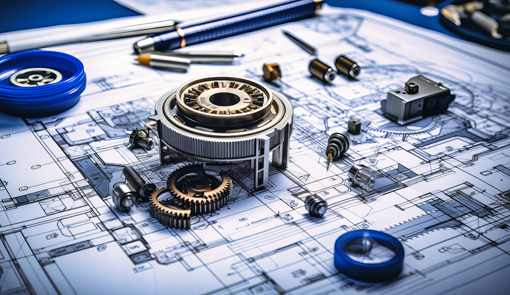
Our expertise spans from preparing comprehensive technical data packages (TDP) to drafting system-level bills of materials (BOMs). We meticulously design validation test plans (DVTs) and ensure seamless system and product packaging, including shipping and handling considerations.
- Prepare technical data package (TDP)
- Complete system-level Bill of Materials (TDP)
- Draft the Design Validation Test plan (DVT)
- Design System / Product packaging and S&H items
- Collect quotes and draft the System-level cost model
- Initiate Reliability review (D)FMEA process
- Evaluate / compare subcontractor(s)
- Identify suppliers for each and every component
- Initiate Quality plan and Delivery Risk analysis on selected suppliers / subcontractors
- Identify alternative suppliers / sources
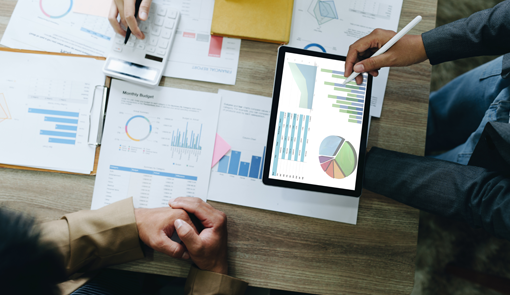
Navigating Product Excellence: From Blueprint to Launch. Our expertise spans from final design reviews to cumulative risk assessment and mitigation strategies. We meticulously release technical data packages (TDP) and secure regulatory approvals.
- Final Design review
- Cumulative Risk Risk Assessment and Mitigation Strategy review
- Release TDP
- Obtain Regulatory Approvals
- Prepare and release product end-user manuals
- Perform complete Design Validation Test (DVT)
- Publish and review DVT results
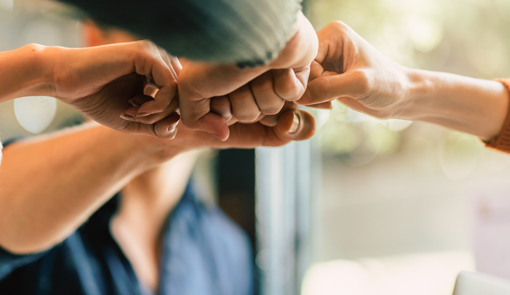
We specialize in facilitating product reliability analysis and reducing performance risks. Our team initiates safety risk mitigation processes in accordance with IAW 5.3 of SO-14971 guidelines. We meticulously select fabrication methods tailored to anticipated production volumes, ensuring efficiency and quality.
- Pre-Launch readiness review with suppliers and sub-contractors
- Follow-up on sub-contractors evaluation
- Initiate Manufacturing / Integration / Testing issues review process (P)FMEA
- Suppliers’ Quality monitoring and Quality Risk mitigation actions
- Suppliers’ performance review
Regulatory framework:
- MedTech
- Aerospace
- Robotics & Microelectronics